Thermocouples are thermometers that are widely used in industrial temperature measurement. They are particularly suitable for measuring high temperatures. But how do thermocouples work? How can you measure temperatures with two simple wires? The key to understanding lies in the Seebeck effect.
Table of Contents
Background
The Seebeck effect, first described by Thomas Johann Seebeck in 1821, is the phenomenon where a weak electric current flows in a circuit of two different conductors when the contact points of the conductors have different temperatures. This connection of conductors is called a thermocouple or thermopair.
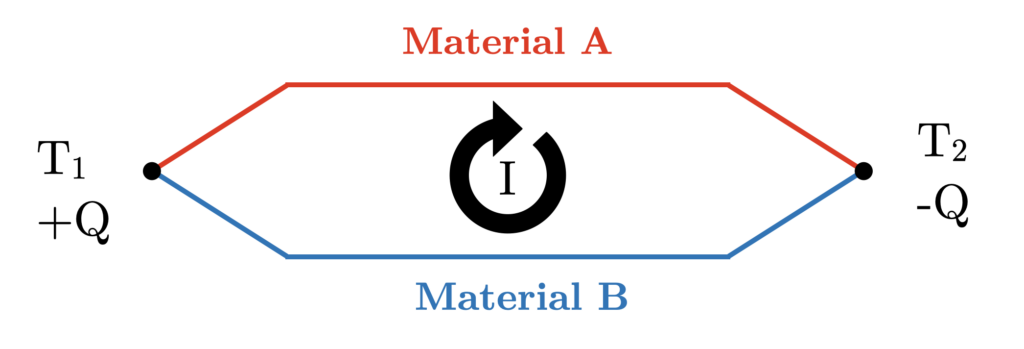
The Seebeck Effect
To understand the Seebeck effect, we can consider a single electrical conductor. Inside the conductor are atoms between which free electrons move. In a state of thermal equilibrium, the free electrons are evenly distributed in the conductor.
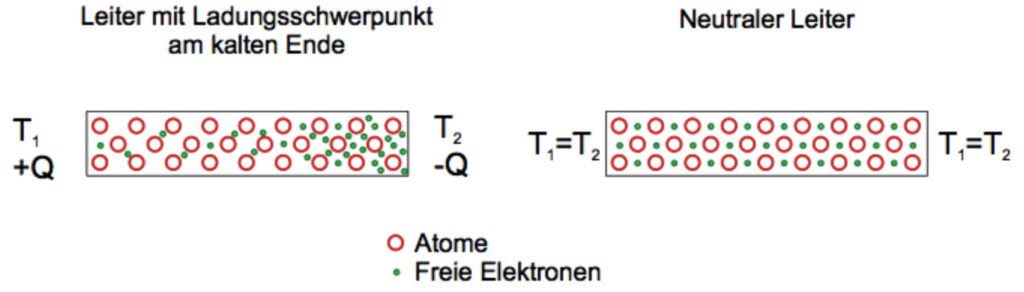
However, when heat is applied to one side of the conductor, the velocity of the free electrons at that location increases. The increased velocity of the electrons displaces them towards the cooler end of the conductor. A charge center develops at this cold spot.
This effect alone, however, does not allow for reproducible temperature measurement, as it is highly temperature-dependent and does not offer a constant relationship between temperature and voltage.
Application of the Seebeck Effect
To achieve reproducible temperature measurement, two different metals with different electron behavior in relation to temperature can be used. When these metals are connected and there is a temperature difference between the junction points, different charge centers develop and a measurable thermoelectric voltage is created.

An example of a thermocouple is the Type N thermocouple, consisting of NiCrSi and NiSi. When there is a temperature difference between the contact points of the two conductors, a measurable thermoelectric voltage is generated, which can be detected with a voltmeter.
Two important conditions are:
- The two conductors must be connected to each other.
- There must be a temperature difference between the junction points T1 and T2.
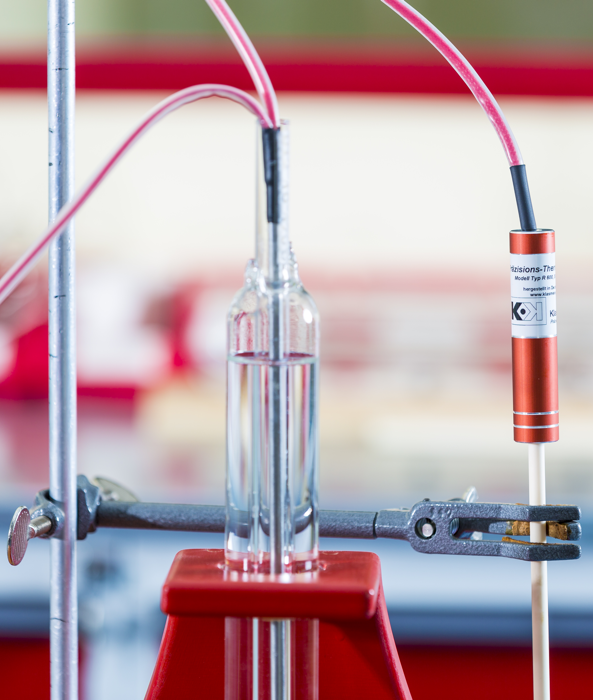
In eigener Sache
Calibration of Thermocouples
Klasmeier offers accredited calibrations according to DIN EN ISO/IEC (DAkkS) for thermocouples. The calibration is performed either at ITS-90 temperature fixed points or by the comparison method in the range of -196 °C to 1200 °C. Noble metal and non-noble metal thermocouples are calibrated, including inhomogeneity scans for accurate measurement results.
Common Thermocouple Types
Thermocouples come in various types, each characterized by the material combination of their wires. Each type has its own advantages and disadvantages as well as specific areas of application. Here are some of the most common thermocouple types:
- Type B (Platinum-Rhodium/Platinum):
- Temperature range: 0°C to 1,800°C
- High temperature accuracy
- Type E (Nickel-Chromium/Constantan):
- Temperature range: -270°C to 1,000°C
- High thermoelectric voltage and good accuracy
- Type J (Iron/Constantan):
- Temperature range: -210°C to 1,200°C
- Not suitable for oxidizing atmospheres above 550°C
- Type K (Nickel-Chromium/Nickel-Alumel):
- Temperature range: -200°C to 1,260°C
- Wide temperature range and cost-effective
- Type N (Nicrosil/Nisil):
- Temperature range: -270°C to 1,300°C
- Better thermal stability and oxidation resistance than Type K
- Type R (Platinum-Rhodium/Platinum):
- Temperature range: -50°C to 1,760°C
- High temperature accuracy
- Type S (Platinum-Rhodium/Platinum):
- Temperature range: -50°C to 1,760°C
- Similar to Type R, often used in the glass and ceramics industry
- Type T (Copper/Constantan):
- Temperature range: -270°C to 400°C
- Good for low temperatures, stable in oxidizing atmospheres
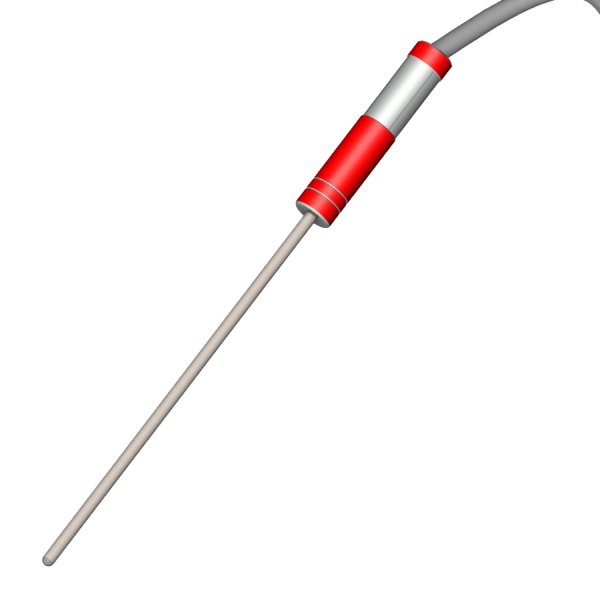
In eigener Sache
Pt/Pd Precision Thermocouple (0 °C to 1500 °C)
The company Klasmeier offers Pt/Pd precision thermocouples with a temperature range from 0 °C to 1500 °C. These are characterized by a voltage-compensating construction, low inhomogeneity, and low measurement uncertainties. The purity of the thermocouple wires is 99.99%, leading to precise and stable measurements. Particularly suitable for applications with high accuracy requirements.
Identification using mini-connector colors
Thermocouples are nowadays indispensable components in many industrial applications and scientific research. Their ability to measure temperatures precisely and reliably makes them an important instrument. The correct identification of thermocouples is crucial for accurate temperature measurement.
One way is to check the color of the connectors and insulation (color codes). Over the years, a variety of different types have been developed, consisting of different material pairings. To enable clear distinction, the various types have been assigned identifying colors. These color combinations are presented in color tables. However, it should be noted that there are different color codes for various countries, for example, those classified according to “IEC” (International Electrotechnical Commission), “BS” (British Standard), or “ANSI” (American National Standards Institute).
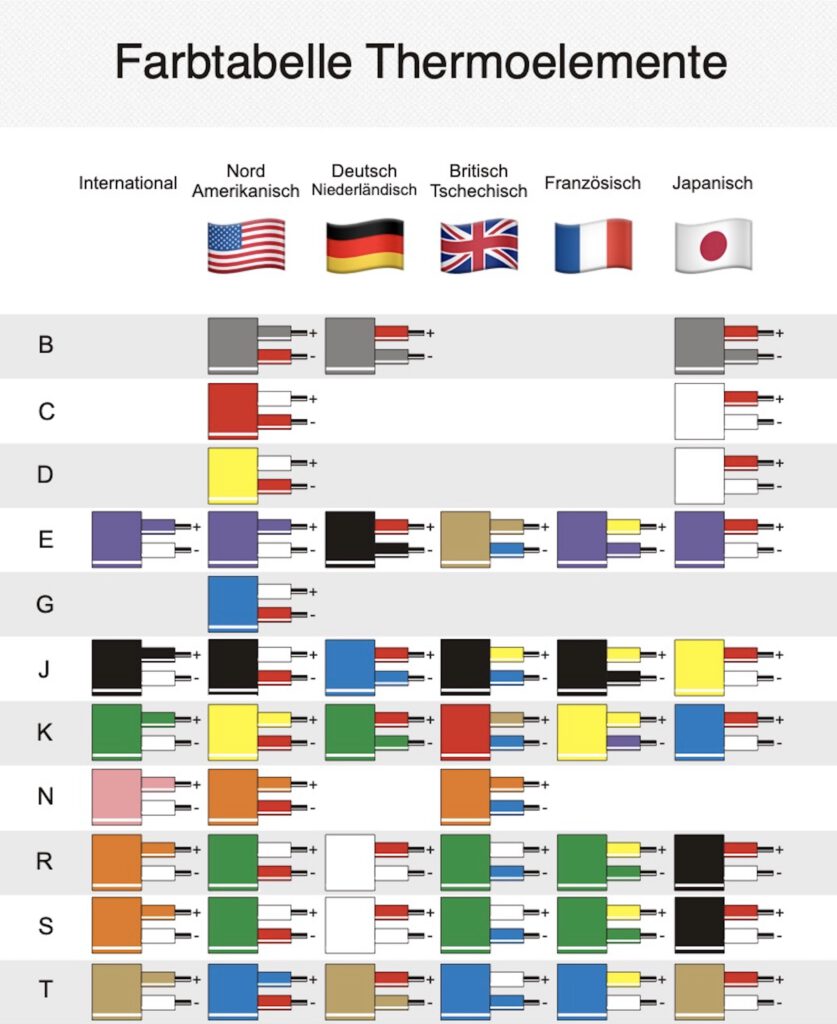
An example of the differences in color coding is Type R. According to the IEC standard, this has an orange insulation, while according to the BS standard, it is marked green. These differences can lead to confusion, especially when thermocouples from different countries are used. It is therefore important to know and consider the corresponding standards.
Below are some common types and their corresponding color codes:
Type K: IEC – green; BS – yellow; ANSI – yellow
Type J: IEC – black; BS – white; ANSI – white
Type T: IEC – brown; BS – blue; ANSI – blue
Type E: IEC – purple; BS – purple; ANSI – purple
Type N: IEC – pink; BS – orange; ANSI – orange
Download color table of thermocouples as PDF:
_
Tolerance limits of thermocouples
Tolerance limits refer to the maximum error or inaccuracy that can occur when measuring temperature with a thermocouple.
The tolerance limit is specified in the IEC 60584 standard for thermocouples and indicates the maximum permissible error that may occur during temperature measurement to still be considered compliant with the standard. The tolerance limit is expressed as an absolute temperature value (e.g., ±1°C) and in the higher temperature range as a percentage of the measured temperature.
There are different classes of thermocouples, each with different tolerance limits. Some examples:
- Class 1: These thermocouples have the lowest tolerance limits and are used for precise measurements.
- Class 2: These are slightly less accurate than Class 1 but are still used in many applications.
- Class 3: These have the largest tolerance limits and are used in applications where accuracy is less critical.
It is important to note that the actual performance of a thermocouple is also influenced by other factors, such as the quality of the materials used, the construction of the thermocouple, and the conditions under which it is used. Therefore, it is crucial to correctly specify and use the thermocouple to ensure that measurements are within the expected tolerance limits.
Tolerance limit Type K
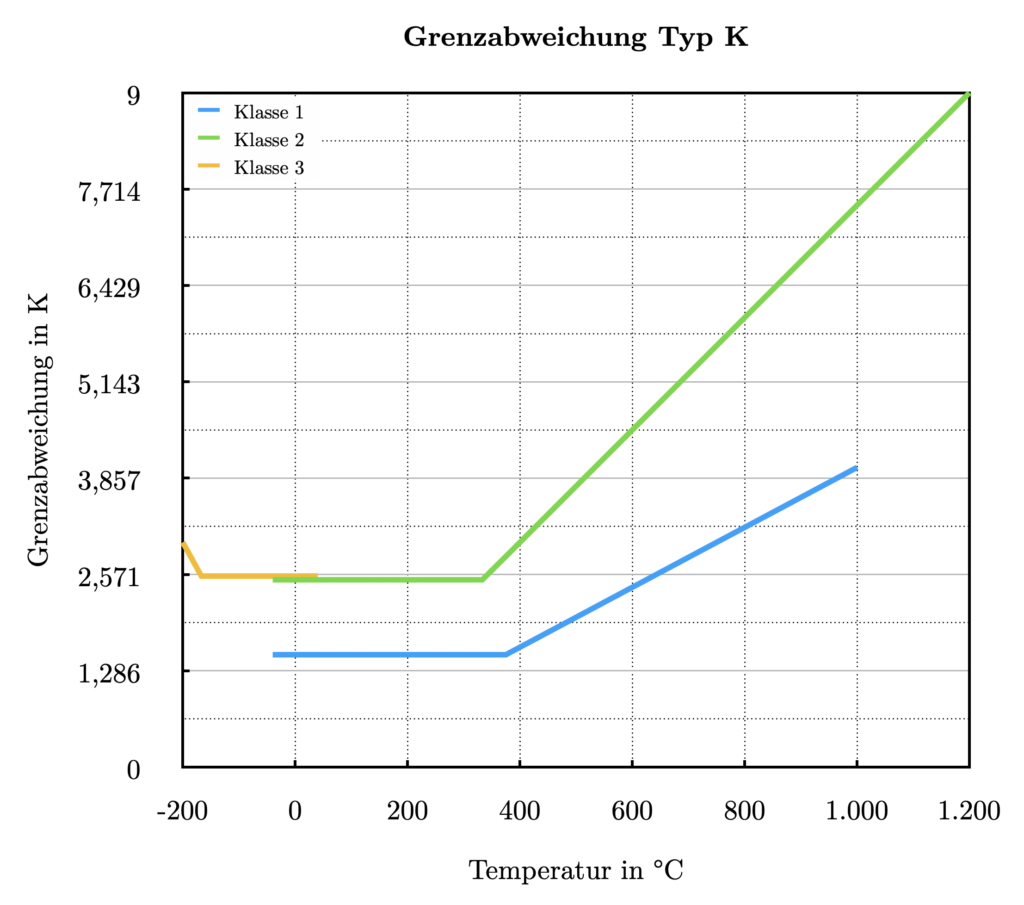
Tolerance limit Type N
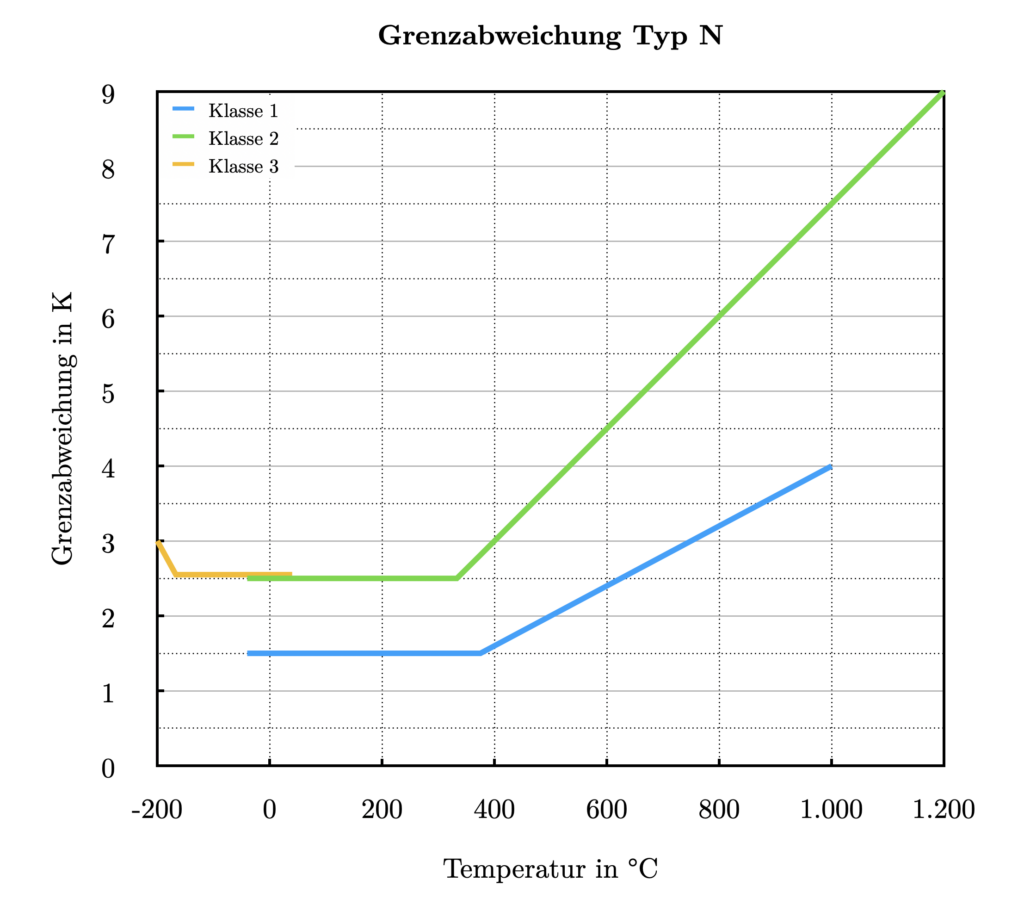
Tolerance limit Type R
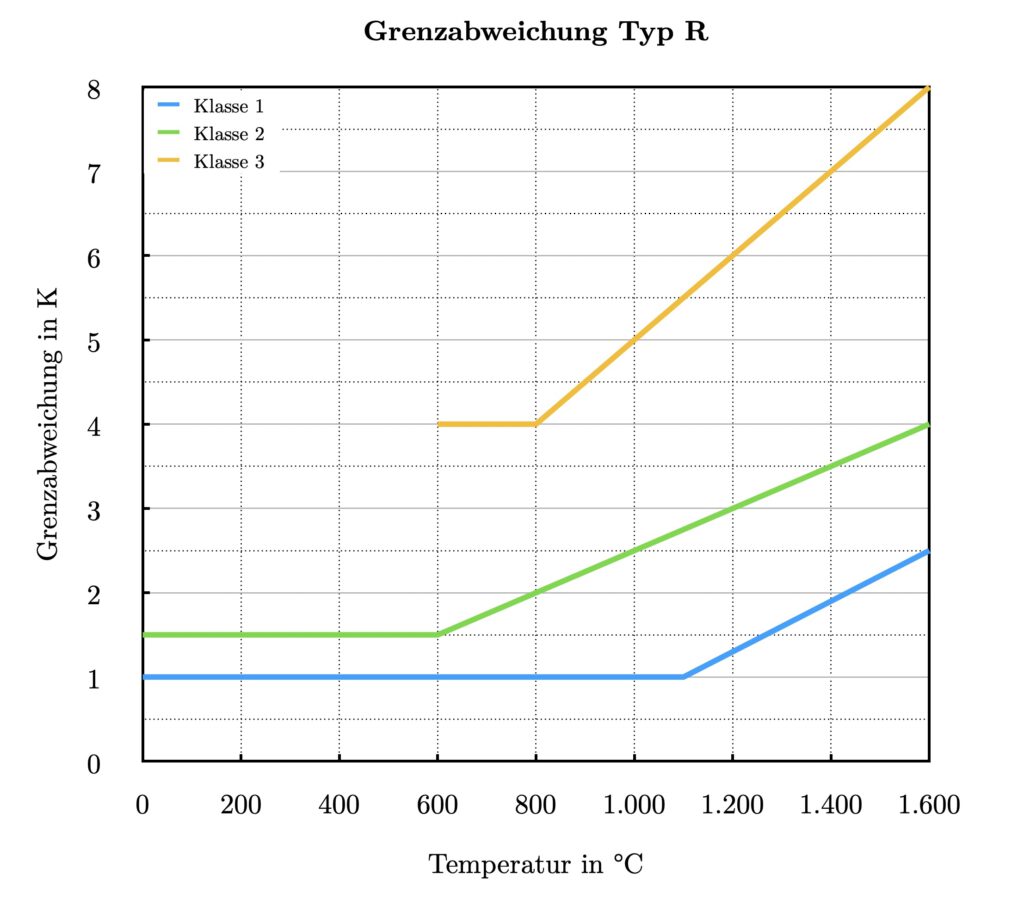
Limit deviation Type S
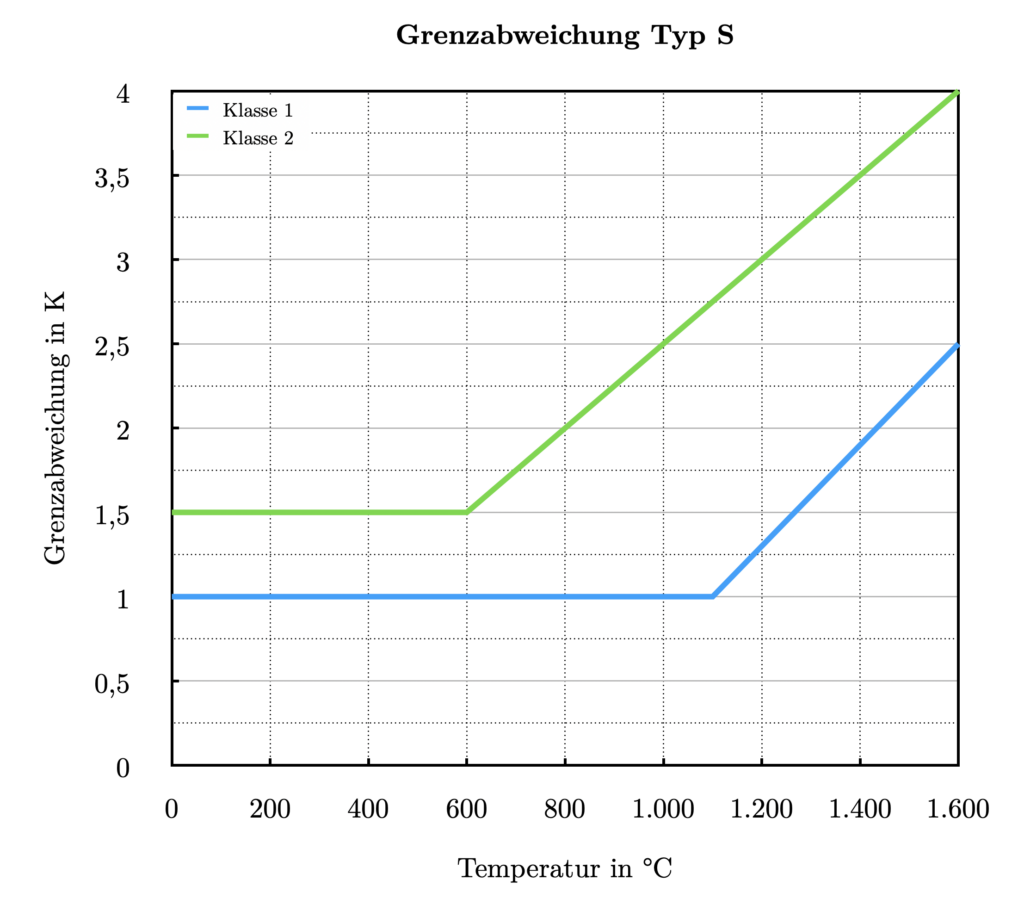
The K-effect of Type K thermocouples
Type K thermocouples, consisting of NiCr and NiAl thermocouple legs, are widely used in industry and offer many advantages due to their ability to be used in an extremely wide temperature range (-270°C to 1372°C) and their high sensitivity at industrially relevant temperatures. However, they are not without flaws, especially in a specific temperature range. This is known as the “K-effect”.
Background:
Although Type K thermocouples can be used in an extremely wide temperature range, they are only reliable in everyday use below 250°C or above 600°C. This is due to a special phenomenon known as the K-effect or Type K state.
The K-effect:
The NiCr leg of a Type K thermocouple has an ordered alignment in the crystal lattice below 400°C. When the element is heated above this point, a transition to a disordered state occurs between 400°C and 600°C. Only above 600°C does the lattice become ordered again.
However, cooling too quickly leads to problems. At cooling rates of more than about 100°C per hour, the crystal lattice does not transform as desired and remains in a disordered state. This can lead to a thermoelectric voltage error of up to 0.8 mV, which corresponds to a deviation of about 5°C.
Interestingly, this K-effect is reversible. Through so-called annealing at temperatures above 700°C and subsequent slower cooling, the lattice can largely be returned to its original state.
Relevance for industry:
Due to this K-effect, Type K thermocouples are unsuitable for measurements between 250°C and 600°C where the temperature changes rapidly. In this range, they can exhibit very large and non-reproducible errors, often in the order of 2°C to 10°C.
Final thoughts:
While Type K thermocouples are widely used in industry due to their many advantages, such as a large operating temperature range and cost-effectiveness, their application range must be carefully considered. In particular, the unreliability in the range of 250°C to 600°C due to the K-effect can lead to significant measurement errors.
It is recommended to consider alternatives such as the Type N thermocouple (NiCrSi-NiSi), which is less susceptible to this short-range order effect due to the alloying of both legs with silicon.
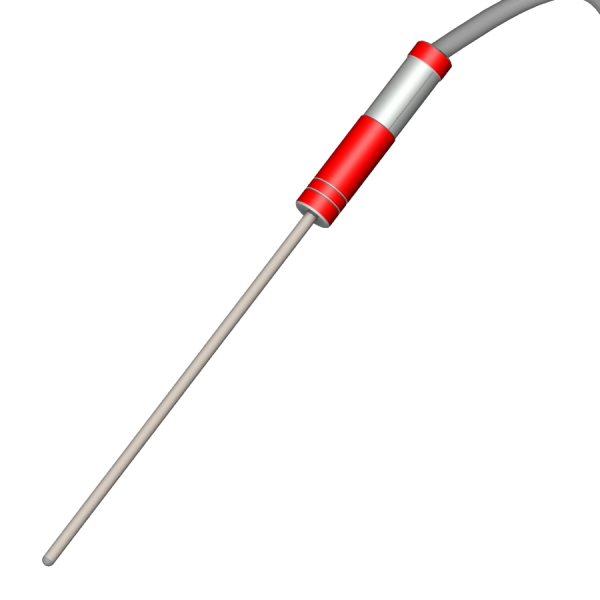
In eigener Sache
Type R Precision Thermocouple (0 °C to 1200 °C)
The Type R precision thermocouple from Klasmeier is suitable for high-precision temperature measurements and calibrations. It features noble metal thermocouple wires of the highest purity and is assembled with a stainless steel reference junction. It can be calibrated at temperature fixed points and offers low measurement uncertainties. The temperature range extends from 0 °C to 1200 °C.
Conclusion
Thermocouples are simple but powerful instruments for temperature measurement. They are based on the Seebeck effect and generate a measurable voltage that depends on temperature. This technology has found wide applications in industry and research, providing a reliable method for temperature measurement, especially at high temperatures.
Sources:
- Frank Bernhard: Handbuch der Technischen Temperaturmessung, 2. Auflage
- Thomas Klasmeier: Table Book “Temperature”, Edition 3