Temperature calibration is a crucial process across many industries, ensuring the accuracy and reliability of temperature measurement instruments. These instruments are used in various applications such as manufacturing, healthcare, research, and energy production. Inaccurate readings can lead to production issues, safety hazards, and increased costs. By comparing temperature measurement instruments to certified reference standards, calibration ensures compliance with quality standards and regulations.
Temperature calibration involves not only verifying the instrument but also validating and documenting measurements to ensure they are traceable and reproducible.
Table of Contents
What is temperature calibration?
Temperature calibration refers to the process of checking a temperature measurement instrument to ensure it delivers accurate and reliable readings. It is compared with a reference instrument, which has a precisely known temperature, to identify any deviations. This process guarantees the accuracy of the instrument, ensuring it performs within the required standards.
Importance and Application in Industry
Precise temperature measurement is crucial in industries such as pharmaceuticals, food processing, chemicals, and automotive. Production processes, storage conditions, and quality control often rely on accurate temperature data. Inaccurate measurements can affect product quality, safety, and efficiency. Regular calibration is essential to minimize errors and ensure compliance with regulations and international standards like ISO/IEC 17025.
Overview of Calibration Methods
Common methods include the comparison method, where the thermometer is compared to a reference thermometer, and the fixed-point calibration, which uses defined temperature points like the triple point of water or the freezing points of metals.
Goals of Temperature Calibration
Temperature calibration aims to achieve several key goals:
- Accuracy: Ensuring that measurement instruments provide precise and consistent readings.
- Safety: Preventing critical safety issues caused by inaccurate measurements, particularly in medical and industrial sectors.
- Efficiency: Enhancing production efficiency by avoiding downtime or quality issues resulting from faulty instruments.
Calibration also ensures that measurements are traceable, meaning they are traceable to international standards and norms for consistency and reliability.
Basics of Temperature Measurement
Different Methods of Temperature Measurement
There are several ways to measure temperature, and the method used depends on the specific situation and how accurate the result needs to be. The most common methods are:
- Resistance Temperature Detectors (RTDs): These measure temperature by detecting changes in the electrical resistance of materials like platinum (e.g., PT100) as the temperature increases.
- Thermocouples: These use two different metals that create a voltage, which changes with the temperature.
Physical Principles Behind Temperature Measurement
Most temperature measurement devices work by detecting physical changes that happen with temperature, such as changes in electrical resistance (RTDs), voltage (thermocouples), or radiation (infrared). These changes are then converted into temperature readings.
Measurement Uncertainties and Influencing Factors
Measurement uncertainties are unavoidable, measurable deviations in results. They are caused by various factors such as the accuracy of the measuring device, external interference, or environmental conditions. Uncertainty defines the range within which the true value of the measured quantity is likely to lie.
In temperature calibration, efforts are made to minimize and clearly define these uncertainties. In Germany, standardized procedures are used, governed by the German Accreditation Body (DAkkS) and the German Calibration Service (DKD), based on the Guide to the Expression of Uncertainty in Measurement (GUM).
The GUM is an internationally recognized document that provides the foundational methods for determining measurement uncertainties. It accounts for both systematic and random errors. The GUM includes mathematical models to calculate and make uncertainties transparent. By following the GUM approach, uncertainties in measurements are documented, ensuring that calibration results are traceable and comparable.
The DAkkS ensures that calibration laboratories in Germany follow the standards and procedures outlined in the GUM and accredits these laboratories according to DIN EN ISO/IEC 17025.
Methods of Temperature Calibration
There are different methods for calibrating thermometers. The comparison method uses a reference thermometer to detect deviations, while the fixed-point calibration uses precise temperature reference points according to the ITS-90 standard to ensure the highest level of accuracy.
Temperature Calibration Using the Comparison Method
The comparison method is one of the most commonly used calibration techniques due to its flexibility and simplicity. In this method, the thermometer being calibrated is compared to an already calibrated reference thermometer.
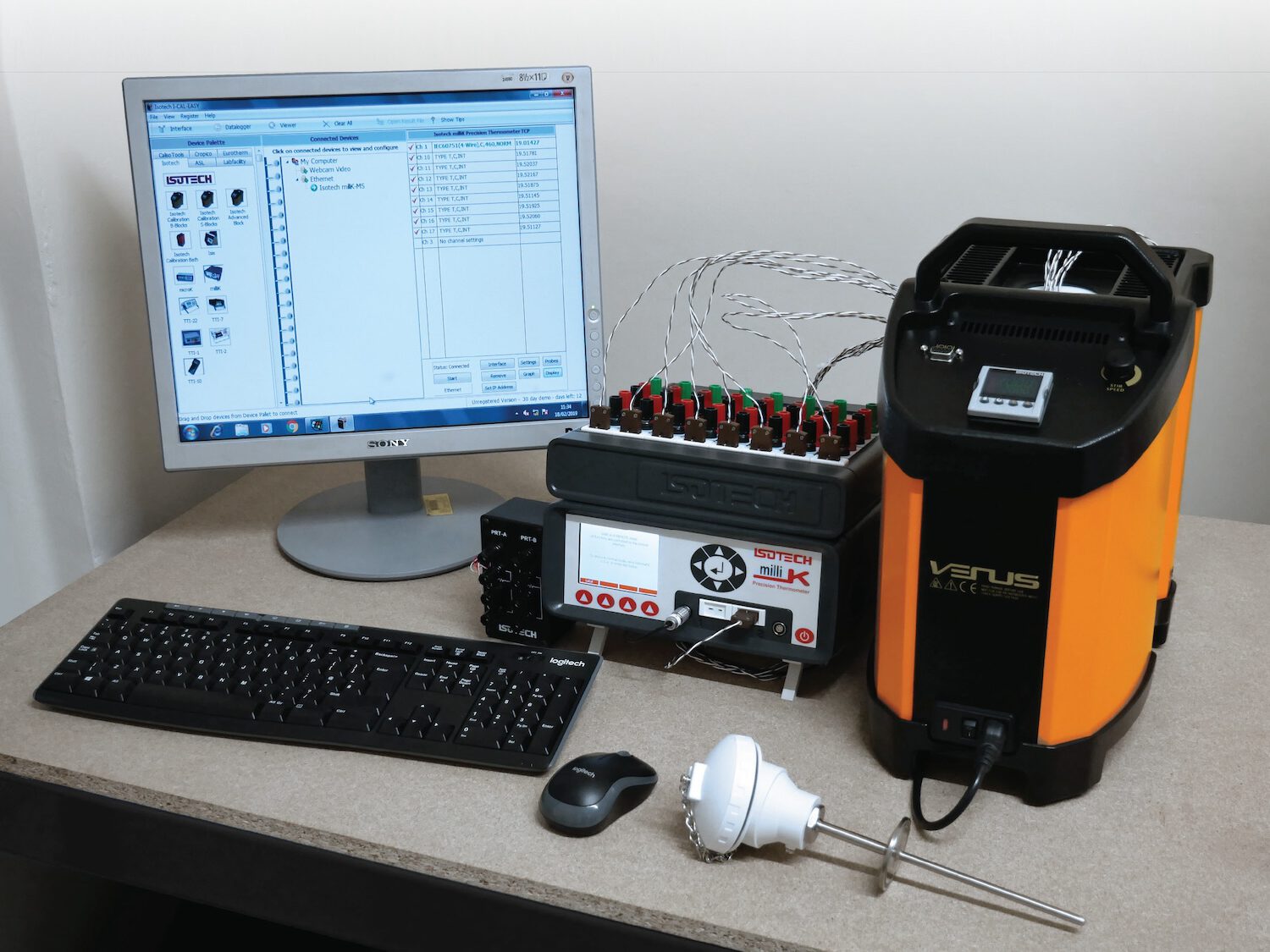
Both devices are placed in a stable environment, such as a calibration bath or dry block calibrator. The difference between the readings indicates the deviation of the thermometer being calibrated. This method is commonly used in industrial applications as it covers a wide temperature range and is suitable for various types of temperature measuring devices.
Temperature Calibration at the Fixed Points of ITS-90
Fixed-point calibration provides the highest precision in temperature calibration and is based on the International Temperature Scale of 1990 (ITS-90). This scale defines a series of internationally recognized fixed points, where physical states (such as phase transitions like melting or freezing) represent exact temperatures. One of the most important fixed points is the triple point of water (0.01°C). In fixed-point calibration, the thermometer is directly compared to these defining temperatures, allowing for extremely precise results.
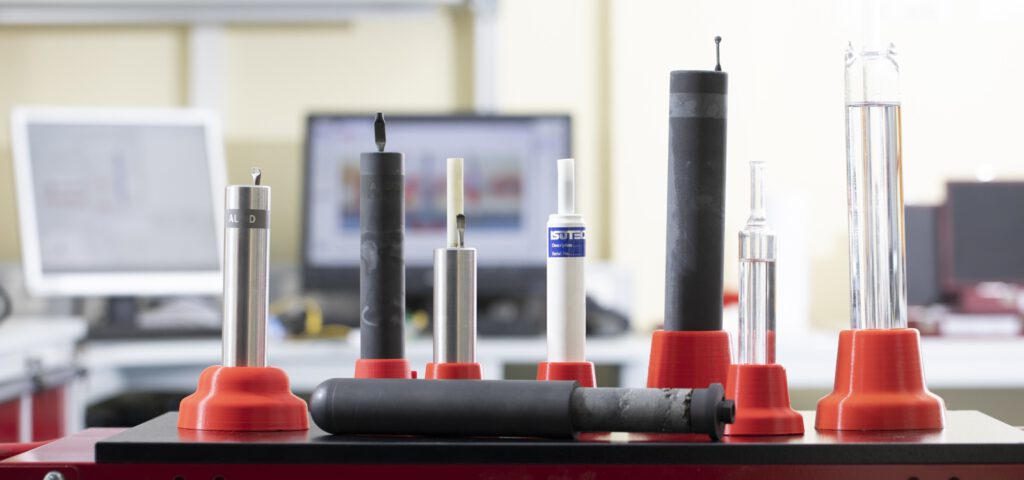
The ITS-90 provides a precise basis for temperature calibration through its fixed temperature points and is primarily used in scientific and metrological applications. The high accuracy and traceability to internationally recognized standards make fixed-point calibration the preferred method for precise laboratory applications. However, due to the complex equipment and specialized conditions required, its use is limited.
The fixed points of the International Temperature Scale of 1990 (ITS-90), used in fixed-point calibration, include:
- Triple point of Argon: -189.3442 °C
- Triple point of Mercury: -38.8344 °C
- Triple point of Water: 0.01 °C
- Melting point of Gallium: 29.7646 °C
- Freezing point of Indium: 156.5985 °C
- Freezing point of Tin: 231.928 °C
- Freezing point of Zinc: 419.527 °C
- Freezing point of Aluminum: 660.323 °C
- Freezing point of Silver: 961.78 °C
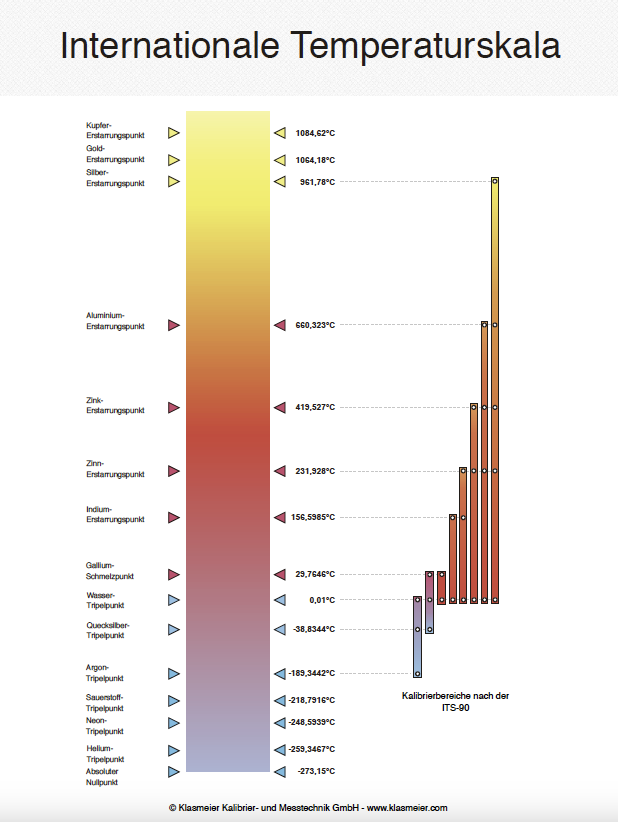
Standards and Guidelines in Temperature Calibration
DIN EN ISO/IEC 17025: Requirements for Calibration Laboratories
DIN EN ISO/IEC 17025 outlines the general requirements for the competence of testing and calibration laboratories. It covers criteria for technical proficiency, the quality of calibration results, and the traceability of measurements. Laboratories accredited under this standard meet internationally recognized benchmarks and ensure reliable measurement results.
More information:
Accreditation under DIN EN ISO/IEC 17025
ITS-90 (International Temperature Scale of 1990)
The ITS-90 defines precise temperature fixed points used worldwide for calibrating temperature measuring instruments. It ensures that measurements are traceable to internationally accepted standards.
Additionally, the ITS-90 specifies the Standard Platinum Resistance Thermometer (SPRT) as the interpolation instrument used between the fixed points. SPRTs offer the highest accuracy and are used as references in precise calibrations to measure accurate temperatures.
More information:
The International Temperature Scale of 1990 (ITS-90)
Importance of Traceability in Metrology
Traceability means that measurement results can be linked back to national or international standards like the ITS-90. This ensures that measurements are comparable globally. Traceable calibrations provide confidence that measuring devices comply with these standards.
DKD Guidelines
The DKD guidelines (German Calibration Service) are a set of technical standards that outline specific requirements and procedures for calibration across different measurement areas, including temperature. These guidelines provide detailed instructions for performing calibrations and evaluating measurement uncertainty. They complement the DIN EN ISO/IEC 17025 standard and serve as practical guidance for calibration laboratories to ensure consistent and traceable results.
The DKD guidelines are particularly useful in specialized areas of metrology, promoting a standardized approach to calibration.
More information:
German Calibration Service DKD
EURAMET Calibration Guidelines
EURAMET (European Association of National Metrology Institutes) is an organization that promotes the cooperation of national metrology institutes in Europe. It sets European standards and coordinates research projects to ensure the accuracy and consistency of measurements across Europe. EURAMET plays a key role in the development of calibration and measurement methods and in ensuring traceability of measurement results to international standards, including temperature calibration. A significant part of its work includes the EMRP and EMPIR programs, which support metrological research.
More information:
EURAMET E.V. – European Association of National Metrology Institutes
Devices for Temperature Calibration
Resistance Thermometers (PT100, PT1000, and SPRT)
Resistance thermometers measure temperature by detecting the electrical resistance of a wire, often made of platinum. The most common type is the PT100, which has a resistance of 100 ohms at 0°C and is widely used in industrial applications.
Another type is the SPRT (Standard Platinum Resistance Thermometer), specifically designed for highly precise calibrations in laboratories. SPRTs are defined by the ITS-90 and serve as accurate reference instruments used in many processes. They are calibrated at the fixed temperature points of the ITS-90. SPRTs provide excellent stability and low measurement uncertainty, making them essential for accurately linking temperature measurements to international standards.
Thermocouples
Thermocouples consist of two different metal wires joined at one end. The temperature difference between the two ends generates a voltage that is proportional to the temperature. Thermocouples are commonly used in industrial applications and are categorized by type:
- Type K (Chromel-Alumel): -200°C to +1372°C, versatile, stable, and widely used. Note: Beware of the Type K effect!
- Type J (Iron-Constantan): -40°C to +750°C, older design, frequently used in industry.
- Type T (Copper-Constantan): -200°C to +400°C, suitable for low temperatures.
- Type E (Chromel-Constantan): -200°C to +1000°C, highly sensitive.
- Type N (Nicrosil-Nisil): -200°C to +1300°C, high stability at elevated temperatures.
- Type S, R (Platinum-Rhodium): Precise noble metal thermocouples with high accuracy.
- Type B (Platinum-Rhodium): Very high temperature range up to +1700°C, used in metallurgy and laboratories.
- Type Au/Pt (Gold-Platinum): Extremely accurate measurements up to +1000°C, mainly used in laboratory applications.
- Type Pt/Pd (Platinum-Palladium): Temperature range up to +1500°C, for high-precision applications.
The more common thermocouples, such as Types K, J, T, N, S, R, and B, are standardized by IEC 60584, which defines thermoelectric voltage tables, tolerances, and temperature ranges for each type.
For specialized thermocouples like Au/Pt and Pt/Pd, the IEC 62460 standard applies. This standard outlines the requirements and thermoelectric voltage tables for these high-precision noble metal thermocouples, used in scientific and metrological applications.
Digital Thermometers / Display Devices
Digital thermometers and display devices are used for the precise measurement of thermocouples and resistance thermometers (RTDs). They come in various accuracy classes and cover a wide range of applications, from simple industrial uses to high-precision scientific measurements.
These devices also need to be calibrated regularly to ensure accuracy. Calibration can be done in two ways:
- Individually (electrically): The digital display instrument is calibrated in isolation.
- As a measurement chain: The calibration is performed with the connected temperature sensor (thermocouple or RTD) as a complete measurement system.
This calibration ensures reliable and traceable measurements.
Dry Block Calibrators
Dry block calibrators are portable devices that generate stable temperatures. They are ideal for on-site calibration of thermometers and thermocouples across a wide temperature range. These devices are flexible and well-suited for industrial applications.
Dry block calibrators are versatile, portable tools specifically designed for the calibration of temperature measurement devices such as thermocouples, resistance thermometers, and digital thermometers. They are made up of a solid metal block, which is either electrically heated or cooled to produce a stable temperature source. The block contains holes where the temperature sensors to be calibrated are inserted.
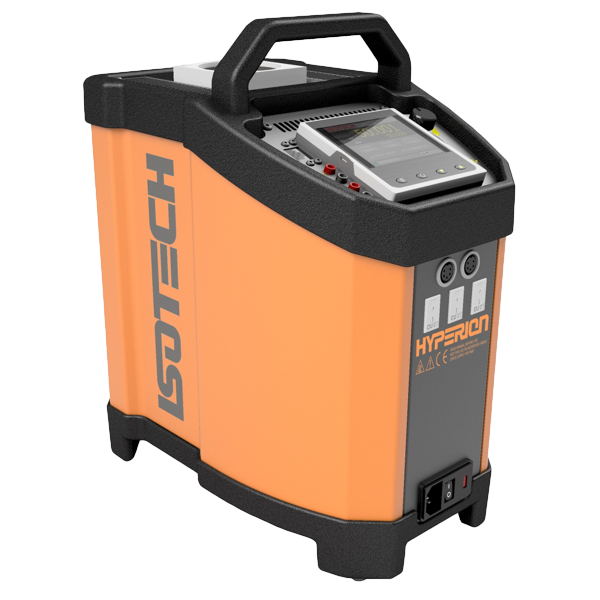
An internal control loop ensures precise and constant temperatures within the block, creating a stable calibration environment. The temperatures generated often range from about -35°C to +1200°C, making them suitable for various industrial and laboratory applications.
Advantages of Dry Block Calibrators:
- Portability: Dry block calibrators are compact and portable, making them ideal for on-site calibrations.
- Wide Temperature Range: They offer great flexibility, as they can generate both low and high temperatures.
- Fast Response Times: They allow quick temperature changes, enabling efficient calibration.
- Ease of Use: Dry block calibrators are often user-friendly, with digital controls for temperature and stability.
- Versatility: They can calibrate various types of temperature measurement devices, including thermocouples, RTDs (Resistance Temperature Detectors), and digital thermometers.
While dry block calibrators are suitable for many calibration tasks, they offer less precision compared to calibration baths or fixed-point calibrations, especially at extreme high or low temperatures. For applications requiring the highest level of accuracy, such as in metrology labs, other methods like fixed-point calibration are preferred.
Calibration Baths
Calibration baths are liquid baths (using substances like oil, water, or ethanol) that provide highly precise calibration for temperature measuring devices. They offer an extremely stable temperature environment and are used in laboratories to achieve greater accuracy than dry block calibrators.
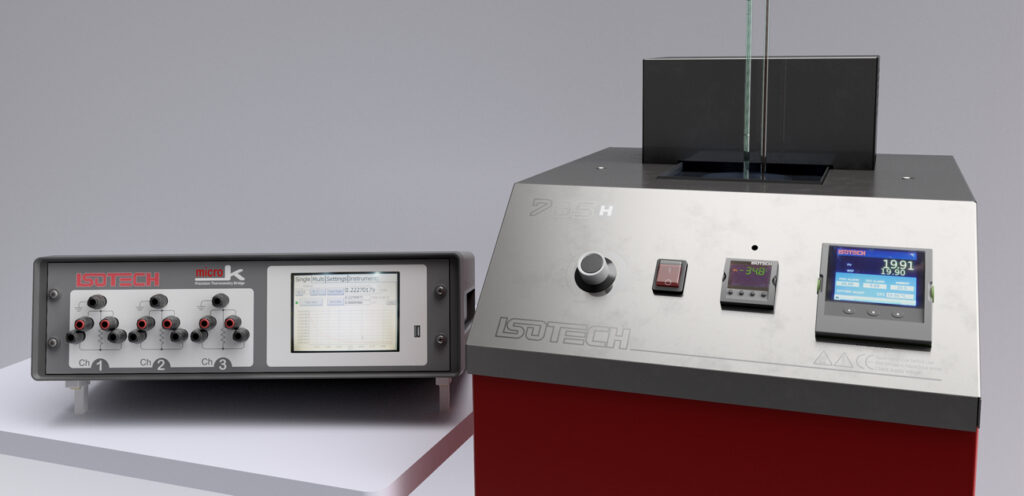
Calibration Furnaces
Calibration furnaces are designed for high-temperature calibrations, often up to 1200°C. They provide a precise, controlled environment for the calibration of thermometers. These devices are particularly suitable for applications where the accuracy of dry block calibrators is insufficient. Calibration with furnaces is less portable than with dry block calibrators and typically requires a specialized laboratory environment. Additionally, they are not suitable for very low-temperature calibrations.
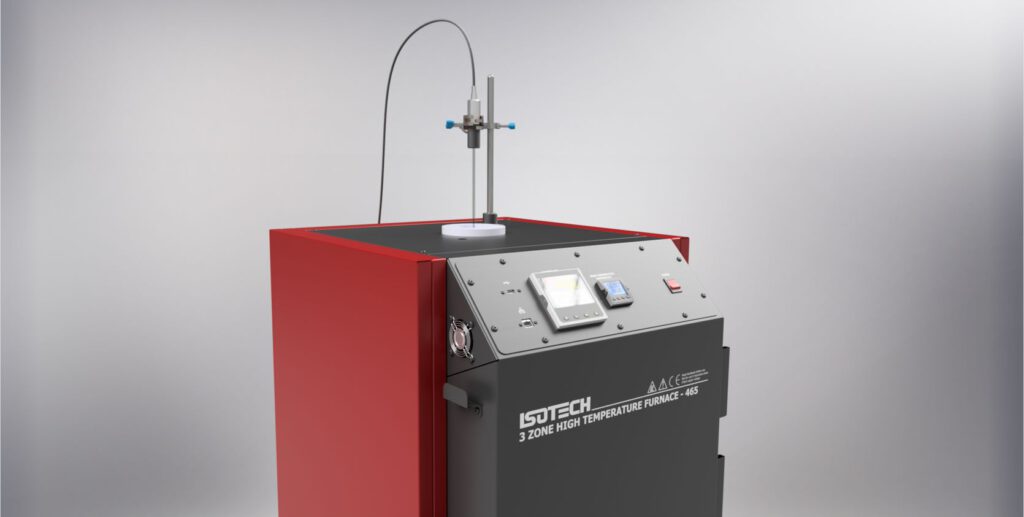
Calibration Furnaces
Calibration furnaces have an electrically heated chamber that provides uniform temperature throughout. The sensors to be calibrated are placed inside the furnace, where they are exposed to a stable temperature for a set period. The temperature is precisely controlled by internal control systems. The thermometers being calibrated are then compared to calibrated reference thermometers to ensure accuracy.